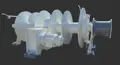
A durable brake motor is crucial for marine deck machinery
Cutting corners can be a costly mistake when it involves electric motors on deck. The harsh marine environment and irregular patterns of use require a motor that is specially designed for the task. Otherwise, there is a risk of critical applications failing when they’re needed the most.
As every mariner knows, there is a world of difference between working above and below the deck. On deck, it is necessary to take precautions for resisting the harsh exposure to the sun, wind and salt water, because these forces can otherwise have severe consequences. This is true of people and machinery alike.
Whereas the vast majority of ship application are below deck, and thus relatively well-protected against the environment, on-deck applications such as loading cranes, winches and anchor/mooring capstans are another matter altogether. The use of a standard electric motor for such exposed application can lead to critical faults. But a specially configured braking motor can handle the task.
“Deck applications are constantly at risk of being inundated by big salt-water waves. When these waves hit the deck with an enormous pressure, seawater permeates everything. This could cause extensive, irreparable damage unless the motor is specially designed to resist this. A motor that operates in a harsh environment like this must be well-protected,” says Maarten de Beun, Sales Manager, Deck Machinery, Hoyer.
Critical deck applications
The additional protection and quality are important because deck applications such as winches, capstans and cranes are often critical for ship operations. In many instances, the machinery must be in good condition in order for the ship’s classification to be valid, and this means that if the motor fails, the ship will not be allowed to leave the port until the motor has been repaired or replaced.
Another factor worth considering is the irregular usage patterns which mean that some braking motors don't run for weeks on end, as winches and loading cranes are only used when a ship is in port or unloading cargo.
“The winches and capstans on fishing vessels are only operating for a few minutes a month. Prolonged periods of inactivity are not good for a motor, so a lot of equipment is needed to ensure that it works when you switch it on. A fault that occurs during the loading of a big catch can be disastrous for the owner of a fishing vessel,” Maarten de Beun says.

Specially built braking motors
Braking motors for deck machinery are almost always specially built for the specific use and application with strict protocols for their assembly. Seeing that we use a modular concept, we can configure the customers’ preferred solution at our own workshop.
An important aspect of manufacturing a specially built braking motor is the assembly of all the different and specially designed components. This makes it important to have skilled employees who are well-trained and know the consequences of sloppy work. Even the smallest components, such as glued seals and O-rings are important to get more operationally reliable motors,” Maarten de Beun says.
Ideally, the cooperation between the customer and the motor supplier starts already during the design phase when the engineers are directly involved in designing the specific application. This makes it possible to take account of factors such as spatial requirements and environmental impact. Hoyer recently updated all of its braking motor drawings so they are available in detailed 3D versions; this enables the customers to place elements such as cables and outlets with greater precision.
Sensors and VFD enhance controls
Whereas relatively simple three-speed motors were previously the most common option for winches and capstans, the market has switched to solutions with variable frequency drives (VFD). Today, most major winch and capstan manufactures use single-speed motors with VFD, which provides a more accurate control and enables precise positioning, at the same time that it exerts a lower electrical and mechanical strain on the motor.
“Some customers simply want to run a 180 Hz motor at full speed to retract a line as fast as possible, but in many applications it’s beneficial to be able to use the VFD to serve as a brake and maintain torque. This is particularly true of winches and capstans that have a more dynamic constantly tensioned utilisation to keep the line taut,” Maarten de Beun says.
Many deck applications also use sensors such as encoders to supply input for dynamic use, such as controlling tension or determining the extent to which a line has been extended. This small, sensitive electronic units need special watertight protection to survive in wet and salty environments.