Pursuing a flawless product
A team of dedicated quality control employees in their production processes and a comprehensive quality system are Hoyer’s strongest weapon in the fight against manufacturing errors. Here, the goal is to ensure that the same fault or defect is not repeated.
Hoyer goes to great lengths to prevent manufacturing errors. Specially trained quality controllers on the production line and a special quality system, called 8D, are some of the most important elements of Hoyer’s quality assurance effort. 8D is a renowned system in the field of quality assurance, and Hoyer has adopted and further developed it.
“The advantage of 8D is that it provides a structured, systematic approach to resolving problems. It raises the level of quality in the identified processes and solutions. The procedure allows us to resolve problems at their root, thereby creating long-lasting solutions. Our approach to quality assurance work is the client's guarantee that if, contrary to expectations, a problem were to arise with a Hoyer product, then we will become actively involved and resolve the problem,” explains Mads Texel Jakobsen, Quality Manager, Hoyer.
Quality on the assembly line
If Hoyer receives a complaint, the case is managed in a clearly defined way via various links in the system, while quality control personnel at factories are on hand to help throughout the process. The company’s approach to a given complaint is, however, situation-specific and solution-orientated, which may mean that the so-called Q supervisors are contacted directly if deemed necessary in individual cases. These Q supervisors are local Hoyer employees trained in accordance with European quality standards and who have their own offices at select factories that manufacture various Hoyer products.
“Our Q supervisors are essential to our quality assurance work because they give us the chance to influence the quality of the manufacturing. The Q supervisors are actively involved in production and perform daily audits of the production processes. Therefore it is often possible to detect potential errors before they are about to occur,” Mads Texel Jakobsen explains.
Involved in product development
The development of the Q supervisors’ role is partly driven by greater customer demands and is partly the result of the further development of the 8D system, which they are now proactively working on to identify the source of faults and correct them. The Q supervisors also provide support from the sidelines when new products are developed. Among other things, this enables the client to perform audits at the factories as part of the product development process.
“The Quality Department and Q supervisors are heavily involved when special products are developed in partnership with our clients. In each step of the project, they assess the quality and make sure that it meets requirements. That’s why they are fully familiar with the specifications and quality requirements and know what needs to be monitored closely when mass production is initiated,” Jakobsen says.
Facts about the 8D quality assurance system
- Recognised problem-solving tool used in the automotive industry and other sectors.
- The purpose of the system is to identify and eliminate the underlying causes of a given non-conformity.
- The system comprises eight steps:
- Establish a team to deal with the problem
- Identify the problem
- Isolate the problem and limit the damage
- Identify the root cause of the problem
- Initiate preliminary initiatives to rectify the problem
- Identify preventive and corrective measures to prevent the problem from recurring
- Verification to ensure the corrective measures have been implemented correctly, are sufficient to eliminate the problem and are upheld
- Conclude and file a report.
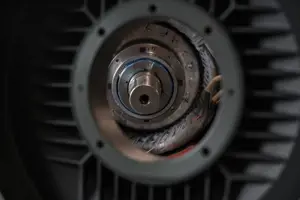