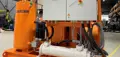
Special compressors built for harsh conditions
Specially-made rotary compressors make it possible for a trio of cement bulk carriers to unload their cargo quickly and efficiently. The engineers at AERZEN Nederland B.V. were faced with a challenge of designing a robust, reliable compressor system that could fit into the limited space on the ships.
Having a pneumatic cargo transport system on board is a big advantage for a cement carrier. Like a gigantic vacuum sweeper, the system sucks up the cement and pumps it out by means of overpressure which enables the ship to quickly unload its bulk cargo without having to depend on the port’s facilities. This reduces the time spent in the port and makes it more flexible for the ship on the routes it is sailing. Another important advantage of pneumatic transport, compared to mechanical cement handling, is that it is completely dustless.
The requirements for reliability and quality for such critical machinery are understandably high. A pneumatic cement carrier system must move enormous amounts of demanding cargo and often do so under harsh conditions. And if the system fails, the ship can neither load nor unload its cargo.
So when the systems integrator needed compressor units for three cement carriers, they contacted AERZEN Nederland which has a comprehensive range of durable compressors and blowers. With seasoned staff comprising engineers and technicians, not to mention testing facilities, AERZEN Nederland has delivered hundreds of customised applications, including specially made solutions for industrial and marine compressors. Thus AERZEN is renowned as a guarantor of reliability.
Durable rotary compressors
The project required a specially-built compressor system to strike a balance between the requirements for output, reliability and size. A standard compressor would usually do the job at most industrial facilities on land, but on board a ship, the scarce space is often worth considering. AERZEN chose their VMX rotary compressor as the basis for the units that were then further developed and built by AERZEN Nederland pursuant to the customer’s specifications. The system will be equipped with a set of blowers that were also developed by the Dutch subsidiary.
“As a long-standing partner of the cement industry, AERZEN is familiar with all the strict requirements on pneumatic transport of demanding bulk goods. Our VMX compressors are highly reliable for this type of purpose all over the world, regardless if it is diesel-power, or as in this case an electric configuration,” says Siert Wiersema, Deputy Manager, AERZEN Nederland B.V.
Orange motors from Hoyer
AERZEN uses six 200 kW IE3 motors from Hoyer to power the compressor systems. AERZEN is convinced that Hoyer will meet their expectations of quality and reliability. And in spite of significant logistic challenges due to the pandemic, the motors were delivered by Hoyer within ten weeks.
“We experienced a rewarding cooperation, technical support and a competitive project price for the six motor units. Hoyer delivered the motors with a special orange colour that conformed to the rest of the system. When we tested the units at our workshop, their output proved excellent, so we see a bright future ahead for these compressors,” Siert Wiersema says.
Facts about AERZEN Nederland B.V.
- A subsidiary of Aerzener Maschinenfabrik GmbH, which has subsidiaries in more than 50 countries and is represented in more than 160 countries all over the world.
- AERZEN has been delivering reliable, high-performance and energy-efficient fans, turbo blowers, axial fans and rotary compressors for industrial purposes all over the world since 1864.
- AERZEN Nederland provides customised solutions to all types of customers, including onshore and offshore compressors, diesel-powered units, vacuum pumps, container units and applications built in accordance with ATEX or NORSOK specifications.
About the motors for this project
- Six 200 kW IE3 energy-efficient marine motors
- Customised shaft dimensions
- B3R installation form
- NU bearings in the drive end
- Special RAL2003 colour